This is what I did:
First I bought good quality double setscrew bearings (the ones without the eccentric lock collars) with the idea of just using the setscrews. Well that didn't work the setscrews kept coming loose and I wanted a tough design and not one that was prone to failure. I liked the thick wall of the race on these bearings so I decided to keep these, but locate the axle differently.
I figured out that with the sprockets in their position I had exactly enough spacing between the sprocket tube and inner bearing to fit a two piece 1 1/4 shaft collars I had purchased (they are a 1/2 inch wide). My idea was to use one of these on either side of the sprocket tube to locate the axle.
Note: Click on thumbnails for large pictures
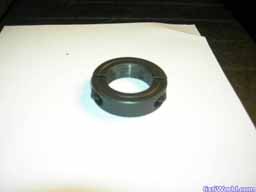
I knew that the sprocket tubes were a bit too long on the outer side for this. I decided to remove the sprockets assemblies to cut the tubes on the outer side to have room for the collars on either side.
To figure out how much to cut off the axle tube: Before I pulled the axle I would remove anything gripping it and leave the sprocket bolt in. Then I would mark the axle on the outside of the outer bearing. I then tapped the axle outward until the sprocket tube touched the inside of the outer bearing. Then I would measure the difference between the mark on the axle and the bearing outer edge. I would now know how much spacing I had and would make up the difference so the 1/2 locking collar would fit. Probably better to cut just a bit (1/16 of an inch) more so you know everything will fit.
The collars cinch the axle and hold it. With both collars inside the machine on either side of the sprocket tube the axle cannot move. It is held in place not only by the collars but also the collar's width combined with the width of the sprocket tube takes up all the space between the bearings. This way if a collar were to loosen up (which hasn't happened) it would still be in place because it's sandwiched between the bearings and the sprocket tube. Also if the axle bolt were to break, the collars will keep the axle in place. This will not happen if you just use spacers.
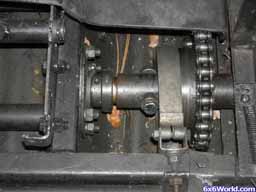
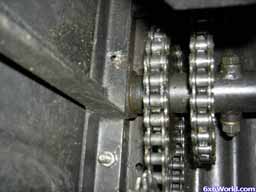
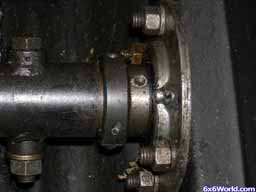
I drilled a hole on the frame over each outer bearing so I can easily put an allen wrench down and loosen the lock collar. Now to remove an axle all I need to do is take the sprocket bolt out and loosen one side of each lock collar and the axle is ready to come out.
This Modification has worked great for a year with no problems. I'm sure it can easily be adapted to different types of machines.
Mike
????? ?????? ???* teen amateur forum
ONION ?????? ?? ???? PHOTO LITTLE GIRL MODELS
outcrydrummer 11-16-2024, 02:22 AM???????: ????*?????? ?????? ? ????????? ???* ??*?????*? (? ??*???? ??*?????*?? ?????? ?? ?*???????)...